Novel HUMS Solution for the Offshore Wind Turbine Industry
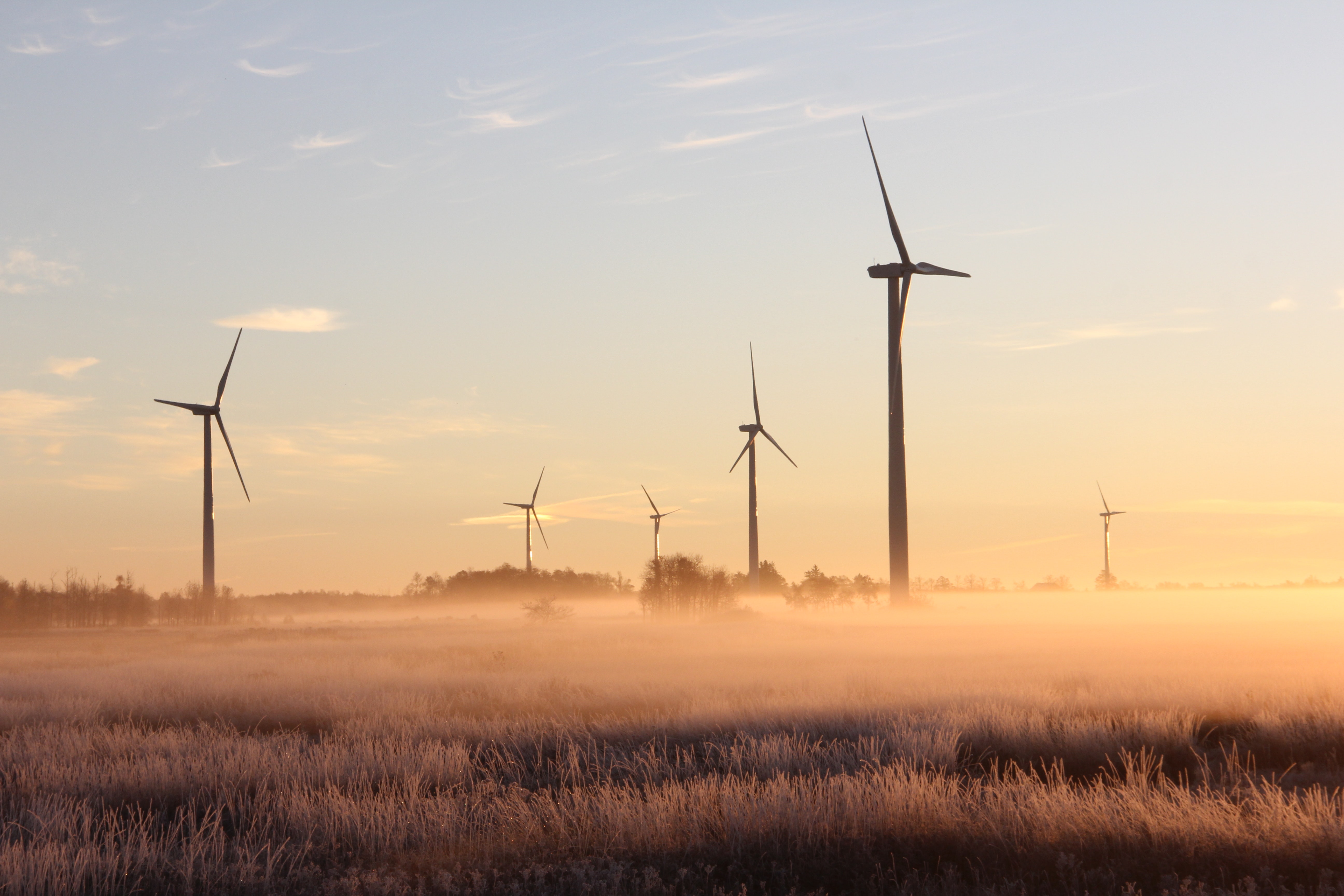
Cost-optimised maintenance of wind turbines is becoming increasingly important due to the remote location and access limitations of offshore wind farms. Maintenance and repair costs increase significantly due to the specialist vessels required and delays due to unfavourable weather conditions.
Wind Turbine HUMS is a collaborative R&D project between Helitune (Beran’s sister company), the National & Renewable Energy Centre (Narec), and the University of Bristol. The project supported by Innovate UK is investigating the transfer of condition monitoring technologies and maintenance models from the aerospace industry to the offshore wind turbine industry. A new health and usage monitoring system is being developed, enabling predictive maintenance and extending component life through the use of advanced maintenance protocols. This will minimise risk for insurers and ultimately reduce the levelised cost of energy.
The experience of the aerospace industry has shown that the remaining life in structural components is governed by extreme transient events. Helicopter operators can elect not to fly in harsh conditions and return them to the comfort of their hangars, but offshore wind turbines are continually exposed to these elements. Both are impacted by dynamic loads, particularly when subjected to rapid changes in wind speed and direction. In addition, wind turbines are affected by yaw misalignment, wind shear across the blade diameter, and turbulent wakes from upstream turbines. These events introduce unsteady loads on the blades that may excite vibrations in critical components and increase fatigue.
The proposed wind turbine HUMS solution will utilise techniques developed by Helitune, for use in the helicopter industry, to measure the impact of rapid fluctuations in wind speed and direction, and assess the impact on the remaining life of key components. The University of Bristol has adapted algorithms used in the aerospace and medical industries for use with wind turbines to enable the detection of transient events in vibration signals. These new solutions are being tested and evaluated at Narec’s world-leading test facilities, see (http://www.narec.co.uk/) in Blyth UK.
Helitune presented a paper at the European Wind Energy Association (EWEA) in Barcelona, to show the results of the first stage of the Narec testing, classifying extreme wind events using the wind turbine vibration signals. Monitoring the exposure of individual turbines to extreme events can identify turbines at greater risk of fatigue due to localised wind conditions or their position within an array. Comparing this information across a fleet of similar turbines over time can inform a predictive maintenance strategy.